Improved efficiency in cold chain management for perishables.
P Company
2023
Agriculture
Challenges in cold chain management led to spoilage and losses. Monitoring tools and optimized storage improved efficiency, reduced risks, and streamlined operations.
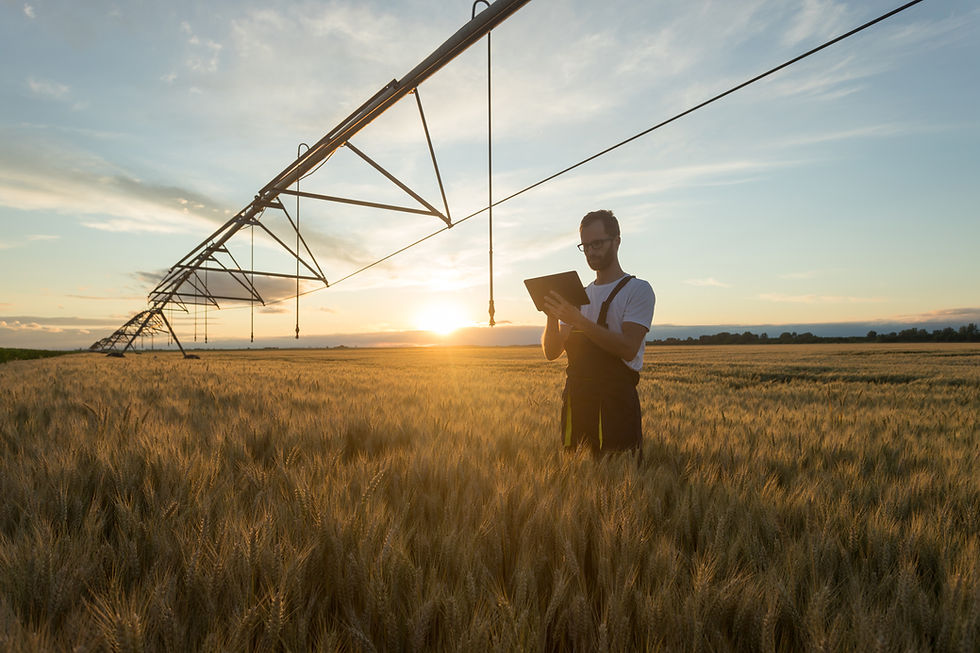
Analysis
Inefficient cold storage increased spoilage risks and operational costs.
Our analysis showed that the lack of real-time temperature monitoring tools and inefficient cold storage practices were the primary causes of spoilage. There was no system to track temperature deviations or address storage issues proactively, resulting in significant financial and operational impacts.

Challenge
Poor cold chain management caused spoilage and disrupted supply chains.
P Company faced inefficiencies in managing cold chain logistics for perishable goods. Inadequate temperature monitoring and suboptimal storage practices increased spoilage risks, leading to financial losses and supply chain disruptions.
Solution
Real-time monitoring tools and optimized storage processes minimized spoilage risks.
Real-time temperature monitoring tools were implemented to track and address deviations promptly. Cold storage practices were optimized by introducing new protocols and staff training programs. A centralized system was introduced to monitor the cold chain process, ensuring timely interventions and reduced spoilage risks.

Maintance
Conducted periodic reviews and updated monitoring tools to maintain cold chain efficiency.
Regular reviews of cold chain performance were conducted to maintain efficiency and identify potential improvements. The monitoring tools were updated periodically to incorporate new technologies. Over two years, spoilage rates decreased significantly, reducing financial losses and improving overall supply chain performance.
Port Insights Advantages
Our Port Insights tool provides all the features you need to make confident planning decisions.

Port Depth
Real-time port congestion data to help you optimize your route selection

Connectivity
Real-time port congestion data to help you optimize your route selection

Berthing Facilities
Real-time port congestion data to help you optimize your route selection

Location and accessibility
Real-time port congestion data to help you optimize your route selection

Equipment and Tech.
Real-time port congestion data to help you optimize your route selection